So the more manganese the better, right? There’s a little more to it than that. It’s true that, within a certain range, the higher the manganese content in an alloy, the harder it will be. This simple relation probably explains the popularity of alloys with a high manganese content over the last few decades.
However, by increasing the hardness of a wear liner you also increase its brittleness. A more brittle alloy is more vulnerable to cracking under high impact. An alloy with a slightly lower manganese content (around 13-14%) will be more ductile and durable, and can therefore absorb more hits without cracking. Depending on the application, harder isn’t always better. Alloys with a high manganese content are especially good for crushing abrasive rocks, but for crushing harder rocks you may be better with a lower manganese content that offers greater impact resistance.
Then there is the presence of other elements in the alloy – carbon increases the hardness and wear resistance of the alloy, and chromium helps prevent ‘metal growth’ (where the liner expands and becomes too large for the crusher). Getting the right ratio of these elements relative to manganese is a delicate balance. Too much carbon or chromium affects the atomic structure of an alloy, stopping it from solidifying into an austenitic microstructure – this would make the alloy far weaker and it wouldn’t have the desired work-hardening qualities.
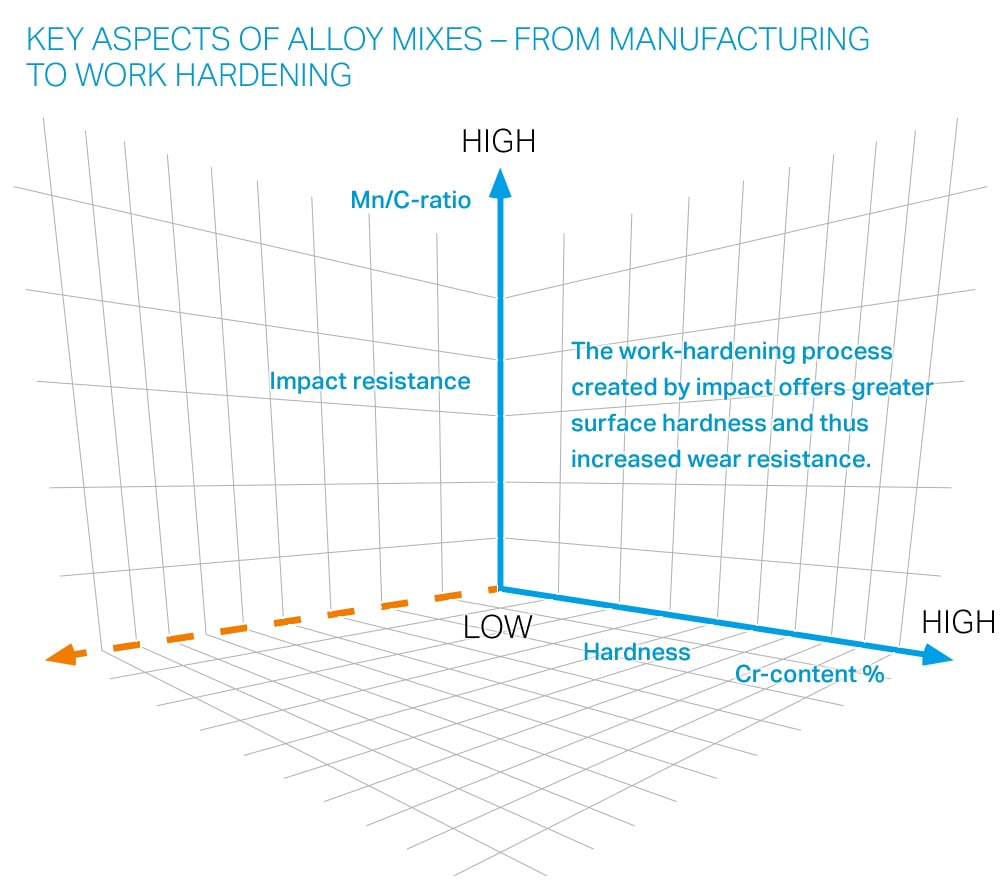