Screening in the mineral processing industries
In the extractive industries, screening is an essential process that – when done correctly – can considerably reduce costs. It is often overlooked, but it offers an opportunity to improve efficiency and return on investment. Therefore it’s important to understand how screening works and how it can help increase the value of your operation.
Mechanical screening should be considered in terms of overall plant economy. For example, better screening can significantly reduce unnecessary crushing, thus decreasing your power usage for crushers and conveyors, and reducing wear and downtime.
There are dozens of factors that can impact upon screening performance – from the type of material to be sorted, to the moisture content, particle size distribution, screening area, screening media, the means of moving the material, and the goals of the screening process. Later in this series, we’ll discuss the impact of these factors in more detail, but before that, it’s important to having a firm grip of the basics.
Firstly, motion is important. If you put a load of material onto a flat, static screen, hoping to isolate fractions of a certain size, you will be disappointed. Without some kind of motion, most of the material will stay in place. When the screen moves, it starts to allow smaller particles to fall to the bottom of the material bed, and pass through the screen underneath. As you continue to shake, the smaller fractions will continue to move to the bottom, albeit at a diminishing rate. The time duration for the shaking to allow the smallest particles to reach the bottom will be roughly proportional to the amount of material on the deck.
This video shows how movement prompts stratification and allows separation to take place.
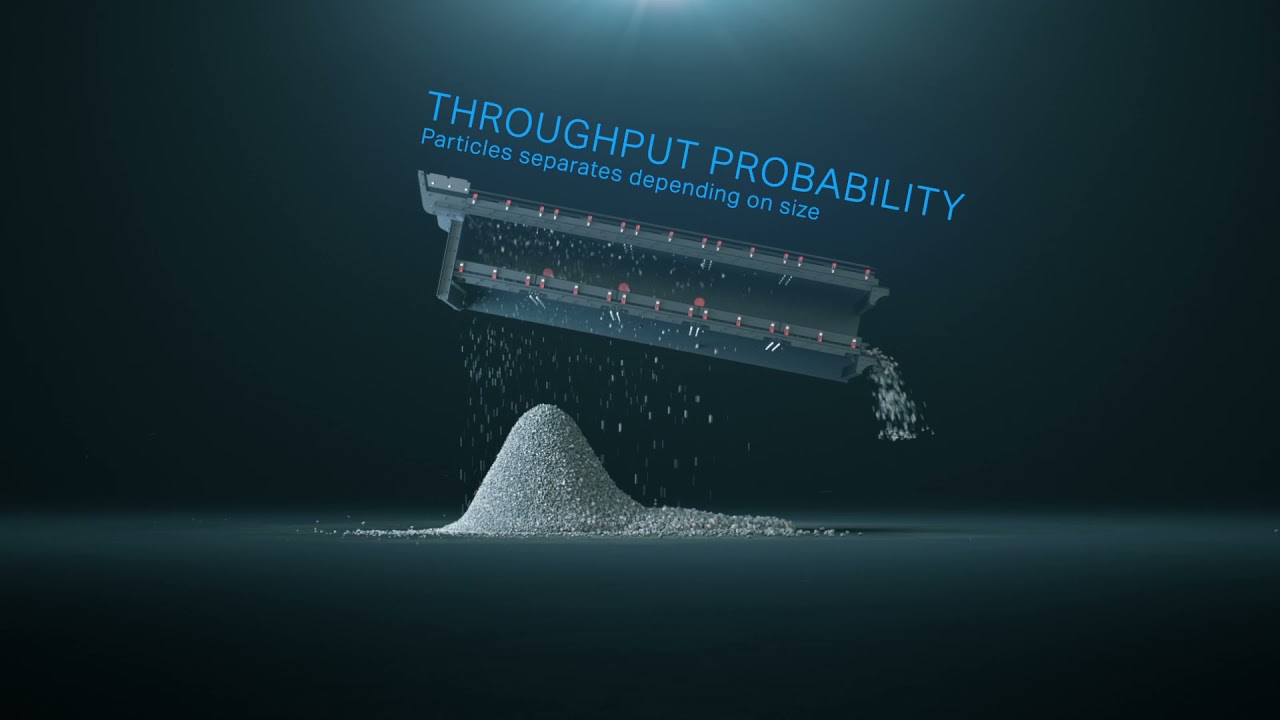
The stratification you can see in the video is a vital part of the screening process, but it’s also important to be aware of free fall separation. If you increase the gradient of the screen (to around 20 to 30 degrees), the material no longer has the chance to build up and form a bed on the screen deck from which to stratify. Instead, the material falls forward and is separated directly on the screening media. This method allows for a higher capacity but less accuracy. Some screens, so called multi-slope screens, combine free fall and horizontal screening to combine the benefits of both approaches and deliver both high capacity and good separation accuracy (for example, Sandvik SF models).
As well as improving accuracy, combining multiple decks inside a single screen can potentially let you separate material into several fractions. You can get an idea of how multiple deck screens operate from the video above. Stratification occurs on both the feed plate and the screening media itself. Smaller, easier to screen particles (higher fines) will be more heavily distributed near the start of the screening process. The majority of near size particles will be screened out closer to the discharge end of the screen.