Stationary cone crushers 800i-series
CS840i
- Nominal capacity
- 212 - 659 mtph (234 - 726 stph)
- Max. feed size
- 431 mm (17 in.)
- Motor power
- 330 kW (442 hp)
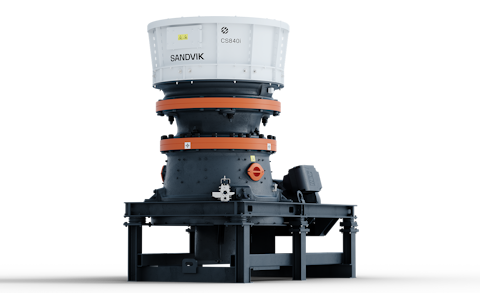
Sandvik CS840i is a high capacity cone crusher for secondary stage crushing.
-
Automation & Connectivity System (ACS)
Automatically adapts the crusher to varying feed conditions ensuring maximum 24/7 performance
-
Hydroset™ system
provides safety and setting-adjustment automatically adapts crusher to feed conditions
-
Unibody mainframe
ensures optimal strength and less maintenance
-
Lifting from above
minimizes risks and allows for safer maintenance
-
Reliability and protection package
Unpredictability is the enemy of productivity. The Sandvik Reliability and Protection package is designed to keep you in control of your costs and efficiency at all times. It includes on-site periodic inspections that enable proactive preventative maintenance recommendations, trend analysis, and our exclusive 1 + 2 years equipment warranty – protecting your investment and giving you an improved cost of ownership.
Product data
- Nominal capacity
- 212 - 659 mtph (234 - 726 stph)
- Max. feed size
- 431 mm (17 in.)
- Motor power
- 330 kW (442 hp)
- Closed side setting (CSS) range
- 22 - 70 mm (1 - 3 in.)
- Eccentric throw range
- 24 - 48 mm (1 - 2 in.)
- Mantles (inner liners)
- A, B, S
- Concaves (outer liners)
- EC, C
- No of chambers
- 2
- Weight
- 25,794 kg (56,866 lb)
- Automation (ACS)
- Included
- Electric dump valve
- Included
- Lubrication tank
- Included
- Tank instrument monitoring system
- Included
- Offline lubrication filtration unit
- Included
Several standard crushing chambers are available for each model. The crushers can easily be matched to changes in production selecting the right crushing chamber and eccentric throw.
The chambers available are:
- EC = Extra coarse
- C = Coarse
Additional product information
With up to 50% higher capacity, 25% increased reduction ratio and a reduced recirculation by up to 50%, with the same amount of high-value end product compared to similar crushers in its class, it is a true super producer. The wide range when it comes to Closed Side Settings, (CSS), together with more and bigger throws, gives you extreme flexibility as the CS840i can be set to fit a huge variety of capacity needs.
It brings you a revolution in intelligent crushing. SAM by Sandvik gives you complete 24/7 access to data generated by your connected Sandvik crusher fleet. Make decisions based on facts, and clearly see areas where you can improve uptime and productivity. Get access to manuals and an e-commerce platform to easily and efficiently buy and reorder wear and spare parts. SAM by Sandvik lets you track & trace parts online to make maintenance planning simpler. No other crushers are better connected.
The CS840i comes with the new generation Automation and Connectivity System (ACS) as standard. The system continuously monitors and optimizes crusher performance and controls the complete lubrication system, increasing uptime and reliability. It can automatically adjust crusher settings to compensate for crushing chamber wear– ensuring consistent product size.
Bolted rather than welded top and bottom shell liners reduce maintenance time and are much safer. It’s 90% faster to change liners compared to welding. The improved over-pressure system with dedicated air channel inlets keeps dust out to increase reliability. The standard off-line filter unit keeps the lubrication oil cleaner with 24/7 fine filtration, reducing wear on your internal crusher components and extending oil life by up to 5 times.
-
SAM by Sandvik
SAM by Sandvik is your digital assistant that gives you the insights, support and performance-enhancing information you need to increase your crushing and screening productivity – all in one place
-
The knowledge hub
Over the last 150 years, we've learned a thing or two about crushing and screening. As innovators and experts in the field, we have a deep understanding of technical and mechanical factors, but there’s more to it than that. Find out at our knowledge hub for crushing and screening.
Contact us
We are present worldwide and always here to help.
Get in touch today!
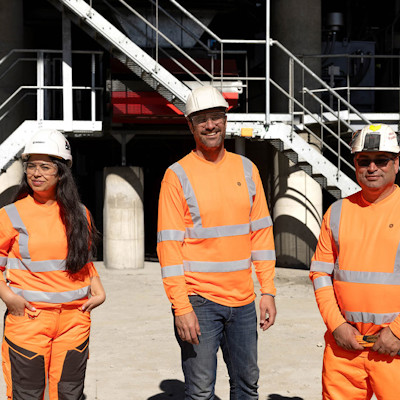