Sandvik delivers ‘Gold standard performance’ at Agnew
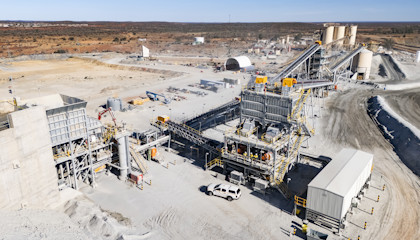
Sandvik has helped global gold producers, Gold Fields, set new standards in efficiency, throughput and operational safety, with the commissioning of a new crushing and screening plant at their Agnew mine in Western Australia.
Gold Fields Limited is one of the world's largest gold mining companies with nine operating mines, located in Australia, South Africa, Ghana, Peru and Chile.
The Agnew Gold Mine is one of four Australian gold mines operated by Gold Fields. The site is situated approximately 375 kilometres north of Kalgoorlie and has a long history of gold production dating back to the late 1970s. The mine is best known for its underground operations, primarily targeting the Agnew and Lawler gold deposits. The ore is extracted using a combination of underground and surface mining and is then processed on-site.
Around 2018, with the mine expanding into a third underground source, there was a need to increase plant throughput. The 21-year-old tertiary crushing circuit, which was suffering from poor reliability, was unable to meet the demand.
Gold Fields Metallurgy Manager - Reg Radford is the company’s technical expert in the field of processing metallurgy. He works with Process Managers across all Gold Fields sites in Australia to assist in optimising the operations. Manager Reg RadfordReg could see that the crushing and screening circuit was not in keeping with the broader standards of the company.
“It was working to its limits, and if you compared it to other Gold Fields sites, it was not to the standard that would be accepted elsewhere,” he said. “It didn’t meet our criterion for a well-organised, safe, professional gold processing operation.”
“The equipment was old, and there was little or no spare parts availability. From a metallurgical perspective, it was being pushed to its limits to deliver the tonnage required. At best it was giving us an 8-10mm output, which was putting pressure on the downstream grinding circuit.”
The age and complexity of the existing plant also meant that access for operation and maintenance was difficult, presenting potential safety concerns.
Seeking a complete solution
The existing crushers were reaching end-of-life, and rather than just replacing them, it was decided to build an entirely new crushing and screening circuit.
To do this, and address various other concerns regarding the existing plant, a comprehensive upgrade project, known as the Agnew Stage 1 Upgrade, was conceived. The initiative examined bespoke and modular designs that could replace the existing plant. The project aimed to improve site water drainage and dust management (by installing a fine ore bin) while minimising disruptions during construction and commissioning.
Gold Fields Manager – Processing, Tristan Freemantle was appointed as Project Director for the upgrade at Agnew. Manager Tristan FreemantleA veteran of the gold and copper industry, Tristan originally worked for Barrick Gold and then transferred to Gold Fields around 12 years ago.
Since then, he has worked across several Gold Fields Australian sites and is currently based at Gruyere, a JV project with Gold Road Resources located in the Yilgarn area of Western Australia.
“Agnew’s mine life had been extended for a further eight years, so upgrading the crushing and screening circuit was important to increase our processing capabilities: we needed to be in a position to process more ore from the new third mine coming online,” said Tristan.
Gold Fields has enjoyed a longstanding relationship with Sandvik, as the company has Sandvik crushers installed at both their St Ives and Granny Smith operations. After considering a bespoke solution, the Gold Fields team chose to go with a Sandvik modular plant.
“We needed a circuit that was simple, low maintenance and reliable, but also wanted the best crushers and screens that we could get,” said Tristan. “Sandvik showed a willingness to work with us within our parameters. Initially, it was just the crushers and screens, but in the end, they presented a complete plant design, which was modular and comparable with the bespoke designs that we were considering.
“Sandvik was also able to accommodate our desire to manage our own electrical and process control design.”
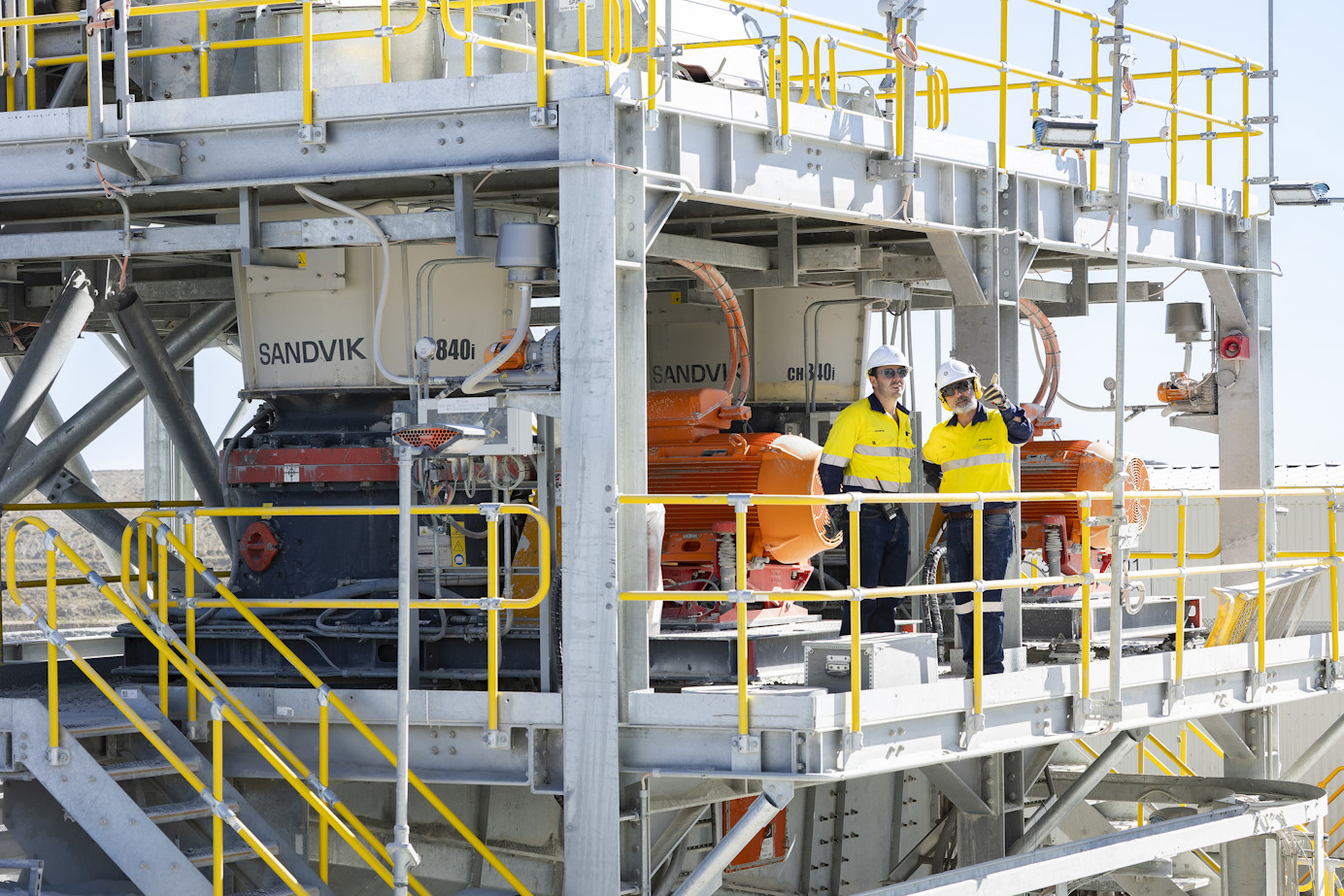
A key to the successful implementation was Sandvik’s expertise in crushing and modular plant design combined with the screening know-how of Schenck Process.
The scope of supply included a Sandvik reciprocating plate feeder, grizzly screen, jaw crusher, and two cone crushers, as well as a Schenck Process double-deck banana screen fitted with Screenex screening media. Sandvik also provided bins, chute work, associated wear protection, and conveyors.
The innovative plant design eliminated the need for two screening stations and associated conveyors when compared with other proposed designs.
“Having a single vendor was an advantage. Sandvik’s initial designs and 3D models were quite detailed and comprehensive, which was encouraging. It gave us confidence in the circuit because we knew exactly how the proposed layout would interact with the existing plant,” said Reg.
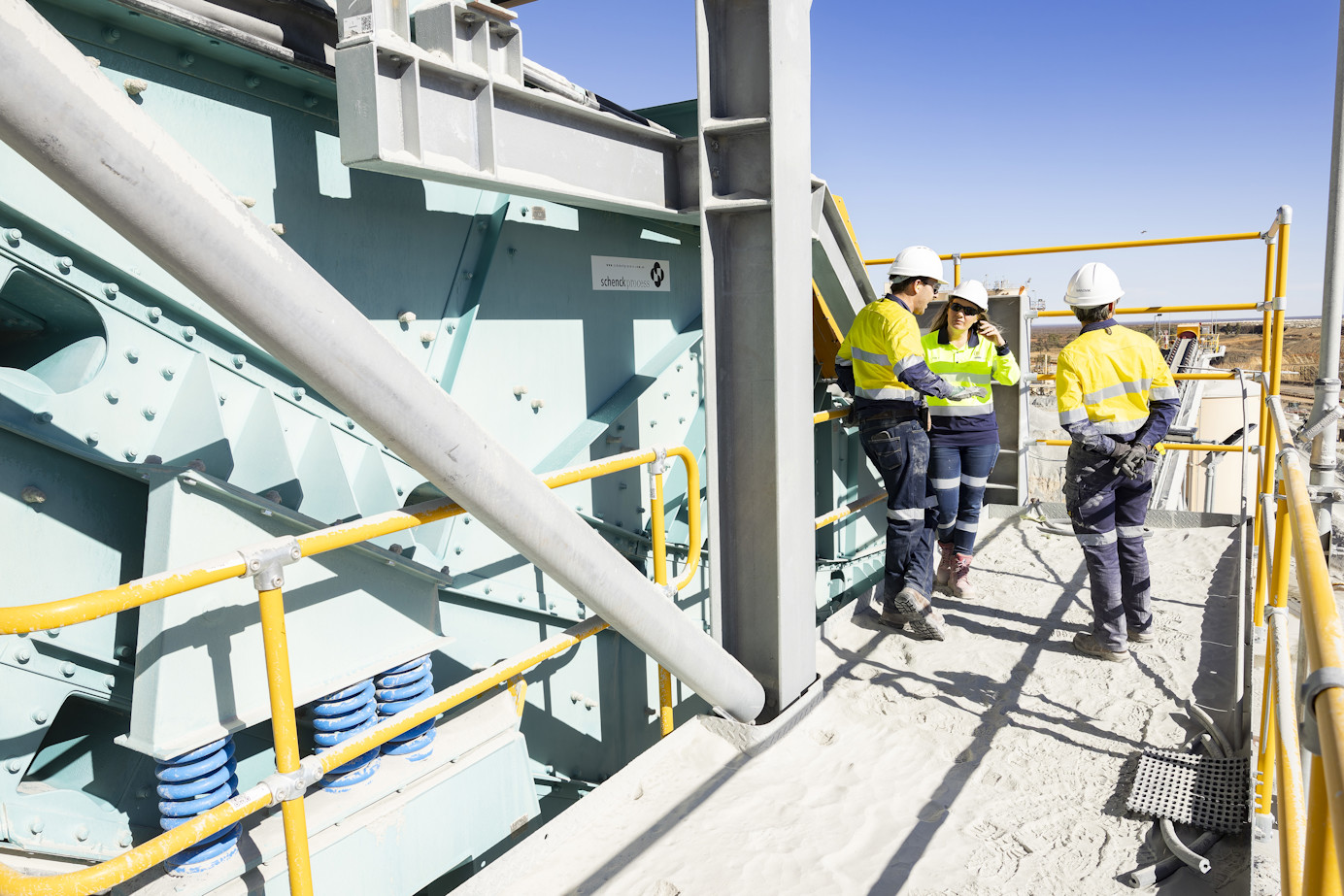
Changeover challenges
A significant challenge for the project team was that Gold Fields needed the new plant to be installed in parallel with the old one so that, ideally, there would be zero downtime.
“Agnew can’t afford to be down for two or three weeks,” said Reg. “The mill is pushed to its limits, so it has little ability to catch up. Solving this problem—where we could build the new circuit and how to tie it in—was a good part of the success story. Commissioning on time and within budget, with limited downtime, was a very important part of the brief.”
To accommodate this requirement, the team decided to move the ROM pad and build the new circuit on the site of the old ROM pad. While this achieved the brief of zero downtime, it introduced a new challenge. The geology of the ROM pad was untested, and some contractors argued that a substantial concrete foundation would be required to support the crushing and screening plant, greatly increasing both the build time and cost.
In the end, working with Gold Fields Geotech consultants, Sandvik’s design team resolved this problem by delivering a support structure for the new circuit that was strong and rigid enough to reduce the concrete foundations required significantly.
Greater efficiency, throughput, and operational safety
The new crushing and screening plant has been running for more than twelve months, and the Gold Fields team is very happy with its performance.
“It is going very well,” said Tristan. The Schenck screen is performing well, and the Sandvik crushers have an intuitive automation system that was easy to integrate with our process control.”
He added, “The new plant was designed for a 2 million tonne per annum (Mtpa) throughput, which is oversized for the current throughput of 1.3 Mtpa.”
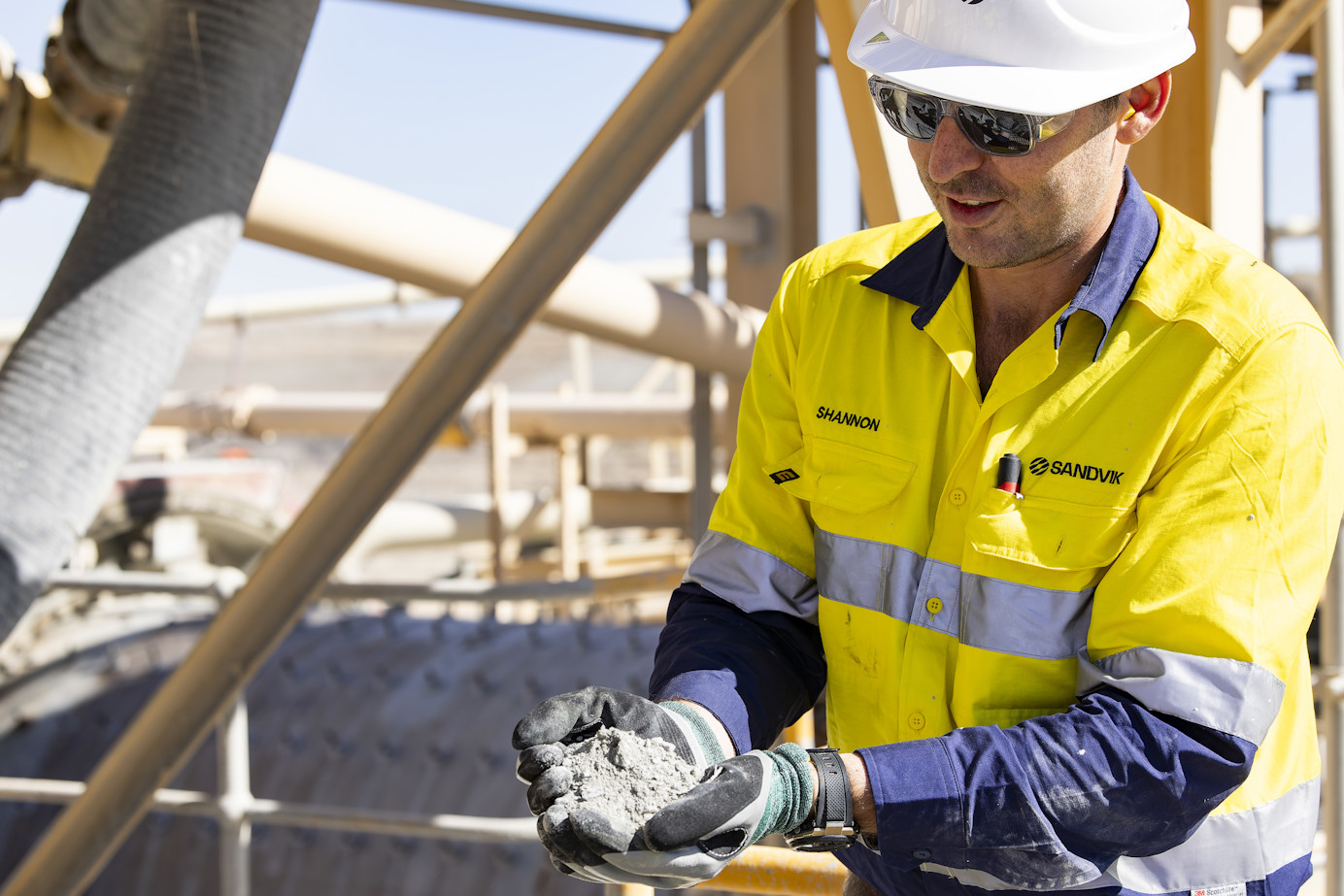
“This means the crushers can be run tighter, producing smaller product. During the design stage, the crusher output was set at 8mm, but it is now regularly producing less than 6.5mm. The finer feed has improved downstream mill performance, increasing the maximum throughput rate from 155 to 170 tph.”
A comminution crushing and grinding survey completed in October 2023 indicates that the new circuit is around 18% more energy efficient than the previous one.
“Also, we were able to centralise the control room duties, where we now have one operator in one control room, and the crushers run pretty much automatically with extensive CCTV around the circuit,” added Tristan.
“Previously, the crushers had their own control room, and the operator relied heavily on visual line of site monitoring.”
Control room operators
Safety has also improved considerably with the simpler design, modern instrumentation, and improved automation. The new circuit effectively addressed safety concerns associated with the old plant, exemplifying Gold Fields' commitment to providing a safe workplace for its employees.
“Access to the new circuit is much easier and safer, with better, wider walkways, chutes that are accessible, and more room for cranes.” said Reg.
Improved Environmental Considerations
According to Reg, the design of the new circuit has reduced dust generation and improved water drainage around the plant.
“The new circuit has fewer conveyors and transfer chutes, and improved water sprays and belt scrapers. We aimed to improve housekeeping and access to make things easier for our maintenance and operations staff. Comparing the two plants is like comparing chalk and cheese.”
Including a fine ore bin seamlessly tied into the main mill feed conveyor reduced dust emissions, reduced freshwater consumption from sprinklers, and improved site drainage through an improved plant layout.
Replacing the crushing and screening circuit has also led to immediate financial improvements for the company.
Financial rewards
The new modular crushing and screening circuit has delivered a minimum annual savings of $1.5 million by increasing throughput at a reduced crushed product size, improving downstream efficiencies, and introducing a fully centralised control room, which has eliminated the need for a permanent second crusher control process technician. Combined with capital savings, this led to an impressive 3-year payback period. The Agnew Gold mine's transformative upgrade not only eliminated long-standing challenges but also ensured a more efficient, cost-effective, and profitable operation.
Teamwork wins the day
The Gold Fields team feels that the teamwork between all those involved has greatly contributed to the success of the project.
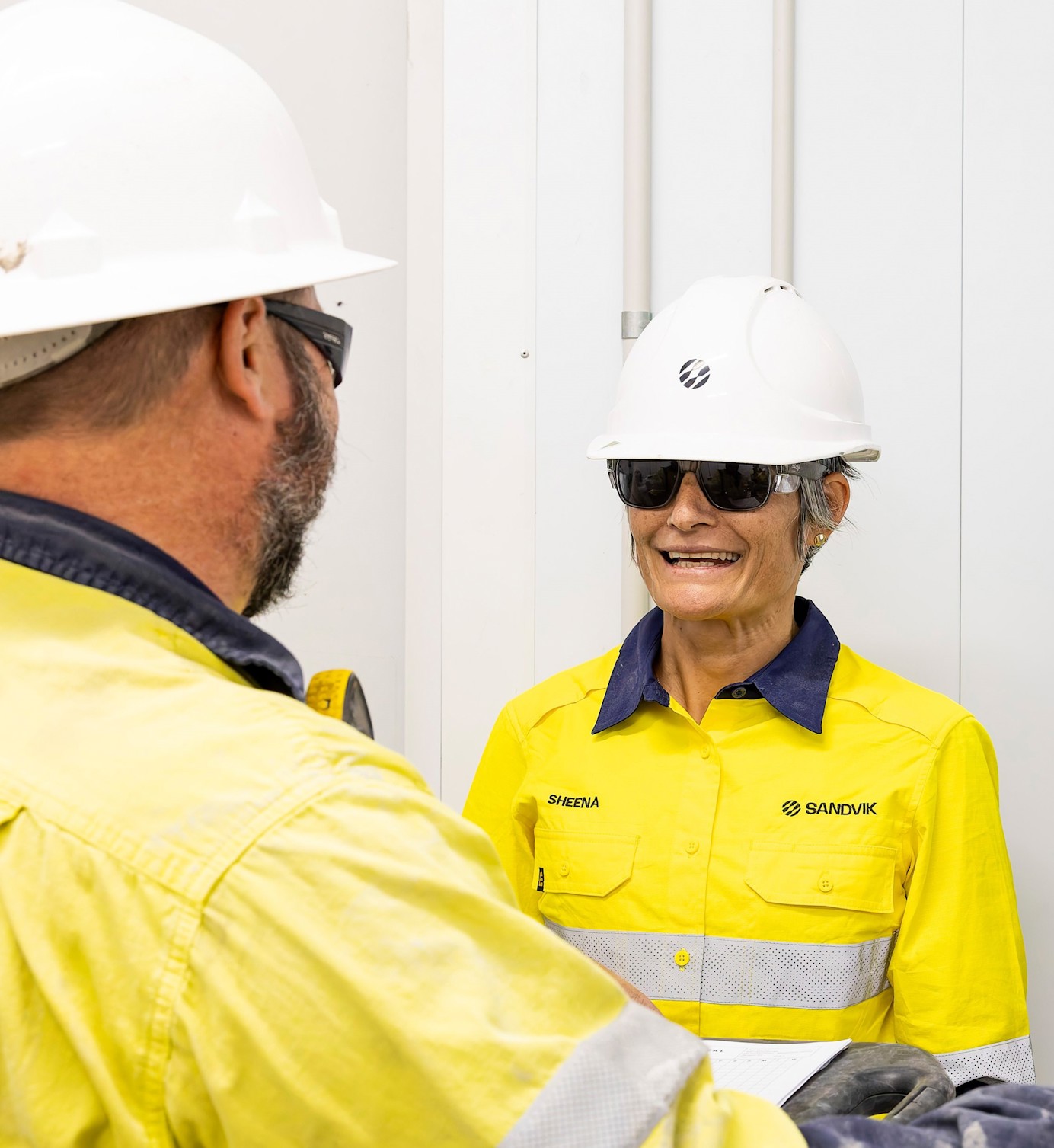
“Overall, working with Sandvik has been quite stress-free,” said Reg.
“There have been challenges on both sides, but we were always able to meet in the middle and find solutions. Once the concrete civil issues were solved, the whole thing came together very quickly.”
“Sandvik’s ability to work with multiple teams was a highlight, delivering a project to spec, and always listening. The Sandvik team really pushed themselves to deliver the project and helped us achieve what we needed despite the challenges – many of which were out of their control,” he said.