Stationary service solutions
Remote monitoring service
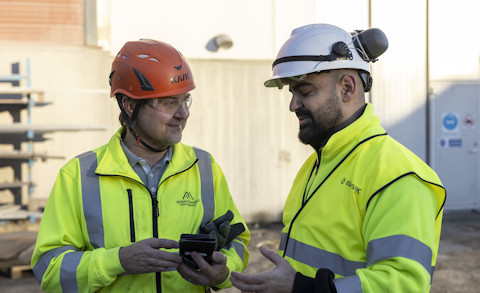
Unlock the full potential of your crushing and screening equipment with Sandvik's Remote Monitoring Service (RMS)
Designed to deliver unparalleled support and expertise, RMS allows you to tap into Sandvik's extensive knowledge in Crushing and Screening technology, providing remote assistance whenever you need it. This service enhances equipment reliability and ensures you receive timely information to resolve issues and resume production swiftly.
Leverage Sandvik's digital platform, SAM, and the expertise of our specialists to receive premium service for all Sandvik cone crushers equipped with ACS-c 5 or ASRi 1 & 2 automation systems.
Monthly data analysis reports
Receive comprehensive monthly reports highlighting major issues, in-depth analysis of crusher utilization, trend analysis, alarms, and efficiency calculations. These reports include recommended actions to address current problems and preventative measures to avoid future issues.
Proactive equipment monitoring
Ensure your crusher is monitored during agreed hours by Sandvik service technicians and experts. Get quick feedback on any abnormalities detected, helping you plan maintenance stops, purchases, and maintain your crushing targets.
Monthly consultation meetings
To work continuously towards improving your application we arrange monthly consultation meetings with your Remote Monitoring technician. We make sure to present our findings and solution to your team and provide additional feedback at your request.
Main benefits with RMS
1. Proactive and reactive actions
- Receive OEM-generated recommendations to solve detected issues and proactive measures to prevent recurrence.
- Address alarms from the automation system, mechanical issues, crusher program, utilization, and equipment optimization.
2. Improved maintenance planning
- Plan maintenance stops with input from Sandvik Remote Monitoring Service technicians, including recommended parts lists and correct spare parts.
- Get detailed pre-maintenance reports highlighting issues or components needing inspection.
3. Continuous access to Sandvik experts
- Gain monthly access to Sandvik crushing & screening experts, ensuring quick resolution of issues.
- Discuss data findings and collaborate closely with Sandvik to keep your top priorities in focus.
4. Increased equipment utilization
- Improve equipment utilization through data analysis and recommended actions from RMS technicians.
- Identify opportunities to increase utilization, minimize idling, and optimize your equipment.
With Sandvik's Remote Monitoring Service, you can ensure your crushing operations are always running at peak performance. Experience the difference with RMS and keep your equipment in top condition.
Remote monitoring service (RMS) boost efficiency at Björkdal gold mine.
See how the new service from Sandvik, Remote Monitoring Service (RMS), together with digital tools through SAM by Sandvik boost efficiency at the Björkdal gold mine in the north of Sweden by enabling proactive work and optimization of the entire crushing process, resulting in a more cost-effective operation and increased availability.
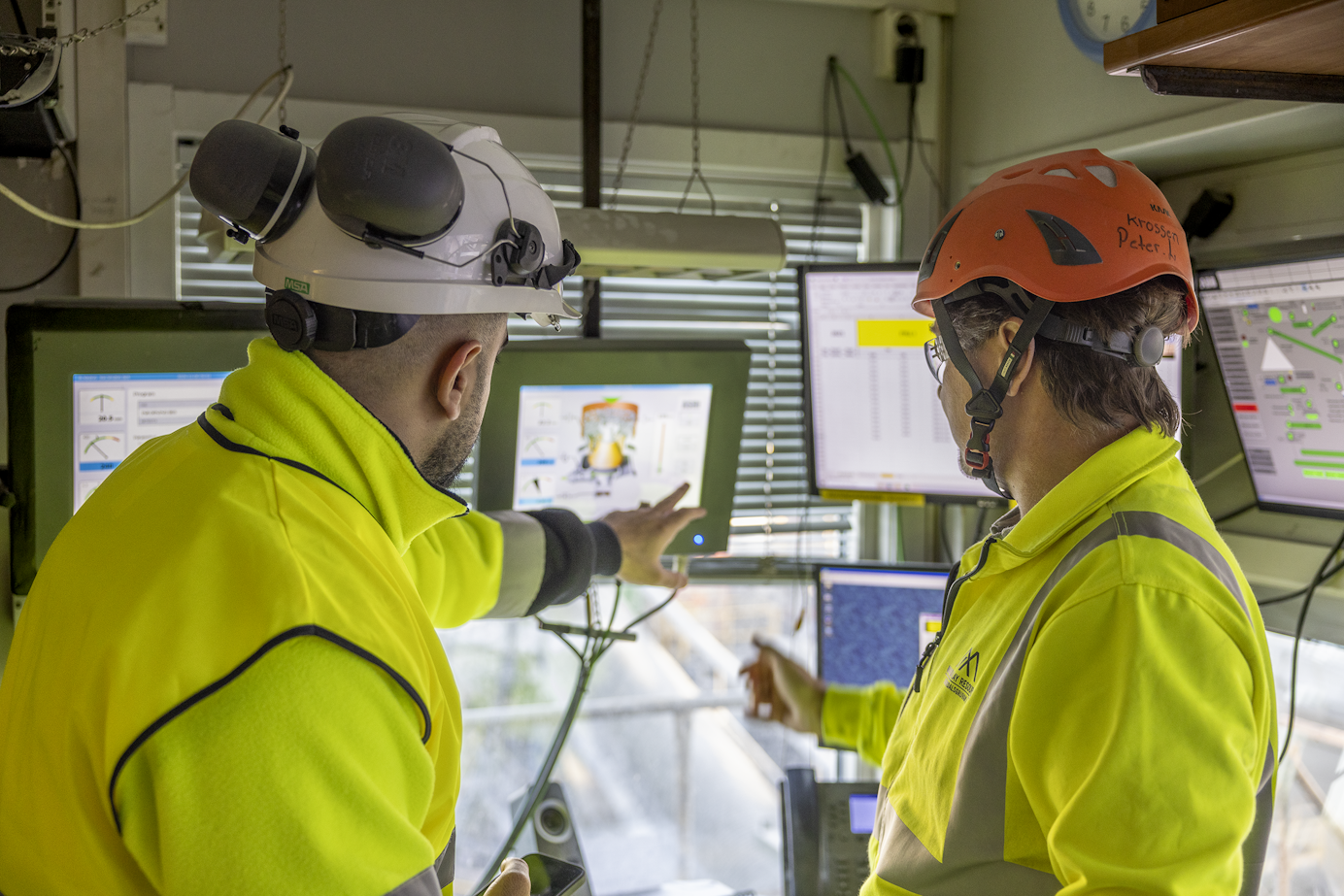
Contact us
We are present worldwide and always here to help.
Get in touch today!
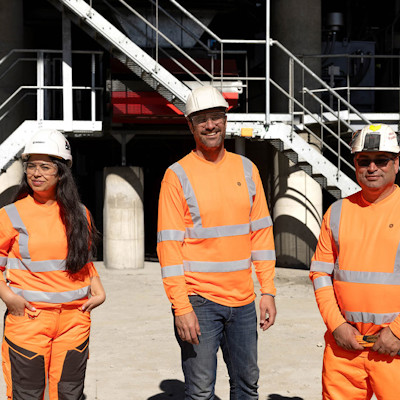