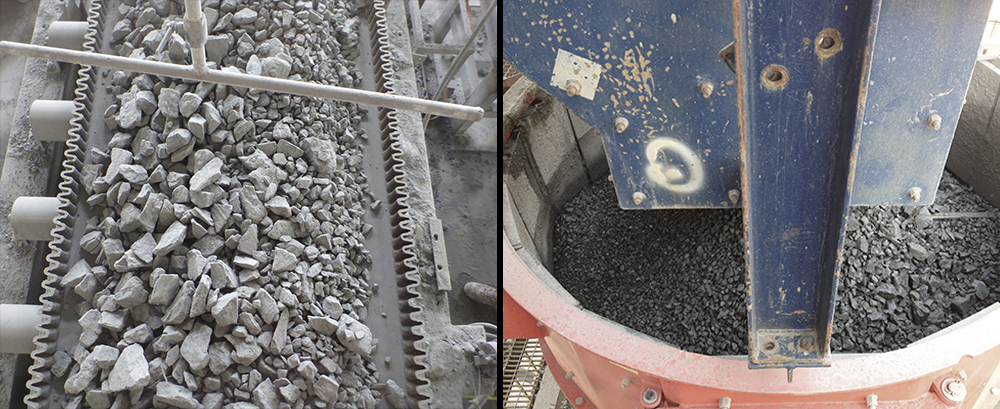
Description: Segregation is when coarse and fine particles enter different parts of the chamber. Typically, smaller particles will accumulate at the bottom of the conveyor and large particles on the top. When fed into the crushing chamber the large particles accumulate on one side of the feed hopper and the small particles on the other side. Also, segregation will occur when material is transferred from one conveyor to another if changing direction at the same time. This will cause fine particles to accumulate on one side of the conveyor and coarse particles on the other side of the conveyor.
Possible solutions: There are a number of ways to address segregation. A feed distributor, splitter, hit plate, tube chute, centering chute, or feeder box could be useful depending on your circumstances. For an optimal solution, Sandvik Rotating Feed Distributor (RFD) can be installed above the hopper to evenly distribute the feed material.